Country
Israel
Application
Pre-filtration to NF
Water source
Process Water
Filtration solution
Stage 1: 5 x 2" Spin Klin™ AAF filters , 70μm
Stage 2: 10 x 2" Spin Klin™ AAF filters, 20μm
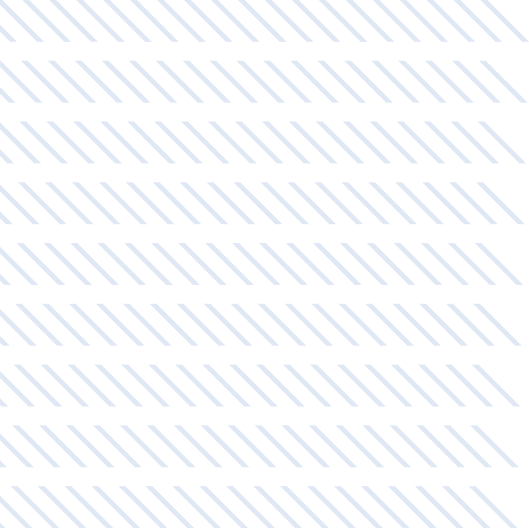
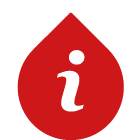
Background
Dairy factories use caustic soda (NaOH) for cleaning the pipes and equipment on the production floor(CIP). This CIP process of caustic soda (pH 12-14) is a built-in process of the production line and is necessary in order to prevent contamination of the dairy products.
In 2004, Arkal (Amiad today) installed 4 units of 2” Spin KlinTM (70 micron) followed by 4 units of 2” SpinKlinTM (55 micron) giving the customer increased CIP stream recovery.
The customer was interested in upgrading the filtration system and bringing the filtration degree down to 20 μm. This would better protect the NF membranes and lead to savings both in cleaning the membranes and their replacement.
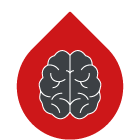
Challenge
The customer needed a system that would successfully filter the precipitant collected by the CIP process, and as mentioned, protect the NF membranes that often get clogged by biofouling.
The new filtration system had to comply with the CIP solution properties (high pH, high salinity, etc.) and cope with temperatures of 40°C, fine filtration and
relatively high and varying loads.
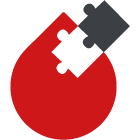
Solution
Amiad supplied a long lasting, cost-effective solution based on its air-aided flushing (AAF) polymeric filters, designed in 2 stages:
Stage 1: 5 x 2” Spin KlinTM AAF filters, 70 micron
Stage 2: 10 x 2” Spin KlinTM AAF filters, 20 micron
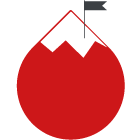
Results
High filtration system performance. The system blocks approximately 90% of all particles larger than 20 microns